Route Cards
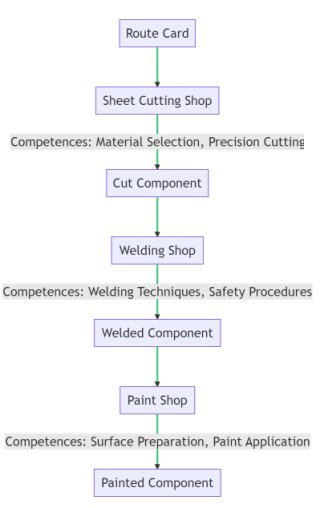
In the context of a manufacturing process, route cards, also known as routing cards or operation cards, are documents that outline the sequence of operations or steps required to manufacture a specific product or component. They serve as a guide for shop floor personnel, ensuring that each step in the production process is carried out in the correct order and according to established standards and procedures. Route cards typically include the following information:
- Product or component identification: Route cards include details about the product or component being manufactured, such as part numbers, descriptions, and any relevant specifications or drawings.
- Sequence of operations: The route card lists the order of operations or steps required to manufacture the product or component, from the initial stage of raw material handling to the final assembly or finishing process.
- Work centres or machines: For each operation, the route card identifies the specific work centre, machine, or equipment required to perform the task. This helps ensure that production resources are allocated and utilized efficiently.
- Operation details: The route card provides specific instructions for each operation, including settings, tolerances, tooling, and any special procedures or techniques that need to be followed. This helps maintain consistency and quality in the manufacturing process.
- Time estimates: Route cards may include estimated times for each operation, which can help with production planning, scheduling, and performance measurement.
- Inspection and quality control: Route cards may also include information about required inspections or quality control checks for each operation, ensuring that products or components meet the necessary standards before proceeding to the next stage in the production process.
- Sign-off or approval: Some route cards require personnel to sign off on each operation upon completion, providing a record of who performed the task and ensuring accountability and traceability within the manufacturing process.
Route cards play a crucial role in managing and controlling the manufacturing process, ensuring that products or components are produced efficiently, consistently, and according to established quality standards. By providing clear instructions and guidance for shop floor personnel, route cards help minimize errors, reduce waste, and improve overall production performance. ExcelWraps offers a digital solution for route cards, transforming the traditional paper-based process into an efficient, easily accessible, and customizable system. The digital route card solution streamlines manufacturing operations, improves traceability, and enhances communication among personnel. Here's how the ExcelWraps digital route card solution works:
- Cloud-based platform: The digital route cards are stored and managed on a secure, cloud-based platform, allowing authorized users to access and update them from any device with an internet connection. This facilitates real-time collaboration and ensures that everyone is working from the most up-to-date information.
- Customizable templates: ExcelWraps provides customizable templates that can be tailored to fit specific manufacturing processes, operations, and requirements. This allows organizations to create digital route cards that accurately reflect their unique production workflows.
- Easy creation and editing: With an intuitive interface, users can easily create, edit, and update digital route cards. This includes adding, modifying, or deleting operations, as well as adjusting work centres, machines, operation details, time estimates, and inspection requirements.
- Real-time tracking: The digital route card solution enables real-time tracking of the production process, allowing users to monitor the progress of each operation and identify any delays, bottlenecks, or deviations from the planned schedule.
- Electronic sign-off and approvals: Instead of manual signatures, the digital route card solution supports electronic sign-offs and approvals for each operation. This ensures accountability, traceability, and efficient record-keeping.
- Automatic notifications and alerts: The platform can send automatic notifications and alerts to relevant personnel when updates are made to the route cards or when specific milestones are reached. This helps ensure timely communication and prompt action when required.
- Integration capabilities: ExcelWraps' digital route card solution can be integrated with existing enterprise resource planning (ERP) systems, manufacturing execution systems (MES), and other software tools, creating seamless workflows and enhancing data sharing and communication across the organization.
- Data analytics and reporting: The digital route card solution generates valuable data that can be analysed and reported on to identify trends, inefficiencies, and opportunities for improvement within the manufacturing process.
By implementing ExcelWraps' digital route card solution, manufacturers can effectively modernize their production processes, reduce paperwork, minimize errors, and enhance collaboration and communication among personnel. This ultimately leads to improved efficiency, productivity, and quality throughout the manufacturing operation.